特注品実例
1リミットスイッチの使用用途について
リミットスイッチは機械の可動部が特定の位置に到達したときに、電気信号を出力する用途で使用されることがほとんどです。例えば、エレベーターでは目的階に到着したときに扉が開きますが、エレベーターの籠が正しい位置に来たことをリミットスイッチで検出して、そこで初めて扉が開くようになっており、籠が移動中では扉が開かないようになっています。
バルブで使用されている電動機や空気圧シリンダのリミットスイッチBOXは、全開位置、全閉位置をリミットスイッチで検出して、制御盤のランプを点灯させます。
手動バルブの場合には、バルブが全開位置又は全閉位置の時に、後の工程を進めるための信号を出す(インターロック)ようにすることがあります。これは、生産機械や生産する商品をダメにしないための方策です。例えば、溶接機には水冷式のものがあり、冷却水を流さずに使用すると壊れてしまうため、冷却水の配管にリミットスイッチ付きバルブを取り付けて、バルブが全開でないと溶接機が稼働しないようにすると、壊れるのを防止することができます。
2ゴム系材料について
1. NBR(ニトリル系)
ブタジエンとアクリロニトリルの共重合体で、耐油性、耐摩耗性がよく、80℃以下では比較的優秀な特性を持っていますが、低温特性は良くありません。Oリングやオイルシールなどのシール材、ダイアフラムや各種パッキンによく使用される一般的なゴムです。「高ニトリルNBR」はアクリルニトリルの量を増やすことで耐油性が向上しますがオゾンには弱くなります。不飽和結合を水素化して飽和結合した「水素化NBR」は、通常品よりも機械的強度や耐摩耗性に優れますが、耐寒性はさらに劣ります。
2. EPDM(エチレン-プロピレン系)
エチレン、プロピレン、ジエンの三元共重合体で、耐候性、耐寒性、耐薬品性がに優れていますが、NBRと違い耐油性は全くないため、油系流体では使用できません。
3. FKM(フッ素系)
耐油性、耐薬品性、耐熱性には優れていますが、耐寒性は劣ります。有機酸、ケトン、エステル、アミン系の薬品には耐性がないため、エンジンオイルなどの使用では注意が必要です。
4. シリコン
耐熱性、耐寒性、耐候性、電気絶縁性に優れ、電気・電子機器や家庭用のシール剤として使用されています。
5. CR(クロロプレン系)
機械的強度、耐候性がよく、NBRに次いで汎用性の高いゴムです。
6. NR(イソプレン系)
「天然ゴム」で、機械的強度や耐摩耗性は優れています。用途としてはタイヤやベルト、靴底などに使用されていますが、シール材には適しません。
7. SBR(スチレン-ブタジエン系)
スチレンとブタジエンの共重合体で、元々天然ゴムの代替用として開発されました。そのため、特性は天然ゴムに近いため、用途も天然ゴムとほぼ同じです。
8. 特殊なゴム材料
従来のゴムの使用範囲を大幅に凌駕する、パーフロロエラストマーと称されるゴム材料があります。「カルレッツTM」という商品名で販売されているゴムが一番有名で、フッ素ゴムの主鎖部(基本となる部分)がテフロンと同じ構造になっています。300℃でもゴム弾性を失わず、耐薬品性もテフロンに匹敵するため、半導体製造装置や食品、医療関係のOリングとして使用されています。
<まとめ>
耐食性:FKM>EPDM>シリコン>NBR
特に、耐塩素についてNBRはEPDMよりも短期間で劣化します。
耐熱性:FKM>シリコン> EPDM >NBR
一般的に、シリコンはEPDMより耐熱性が優れています。
耐油性:FKM> NBR >シリコン> EPDM
NBRは比較的耐油性が高く、逆にEPDMは耐油性が全くないため注意が必要です。
※ゴム系材料の欠点
ゴム系材料は、何かの特性を強化すると別の特性が劣化することがあるため同じ材料でも注意が必要です。例えば、耐熱性を良くすると耐寒性(低温での特性)や機械的特性が悪くなるなど。
3フッソ樹脂について
フッ素樹脂は、耐薬品性、絶縁性、低摩擦性、非粘着性に優れた樹脂です。四フッ化エチレン樹脂(PTFE)がデュポン社で1938年に発見され、当時は第二次大戦前であり、軍の機密情報として公にされませんでした。大戦後、特許の関係から、各社で同じような四フッ化、三フッ化系樹脂が個別に開発されました。ちなみに、テフロン(Teflon)TMとは、ケマーズ社(デュポン社から分離)の製造するフッ素樹脂の登録商標で、「○○フロン」といった同様の名称を、各社が登録商標としました。
1. PTFE(四フッ化エチレン)
フッ素樹脂の一番グレードの高いものです。加熱しても溶融しないため、粉末を圧縮成型→焼成してから、切削して製作します。RPTFEは、強度を増すためにガラス繊維やカーボンを添加しており、通常は白色ですがカーボン入りは黒色になります。
2. PFA(四フッ化エチレン パーフルオロアルキルビニルエーテル共重合体)
PTFEを溶融成型できるようにしたもので、特性はPTFEとほとんど同じですが半透明色です。
4摩擦圧接について
1. 摩擦圧接の歴史
摩擦圧接(FRW)は接合する金属同士を高速で擦り合わせ、発生した摩擦熱により母材を軟化させると同時に圧力を加えて接合する技術です。接合面での激しい塑性流動のために固相接合とすることができ、結晶の粗大化や金属間化合物が生じにくい特徴を持ちます。
摩擦熱によって接合をおこなうという考え方は古くからあります。1891年にはイギリスで圧接の方法が考えられ、1920年代のイギリスとドイツで線形摩擦接合(LFW)が発表されました。LFWは材料同士を荷重で押し付けながら上下方向に振動(線形運動)させた際に生じる摩擦熱を熱源とした接合法です。しかし、これらの手法は当時はまだ実用化とは至らず研究・考察が中心でした。
摩擦圧接が注目されるきっかけとなったのは、旧ソ連で1954年に回転摩擦接合(RFW)の実験が成功し、1957年にMST-1という摩擦圧接機が発表されたことです。翌年、旧ソ連やチェコスロヴァキアが工場への導入をおこなう中で、非ソ連影響下の各国でも実用化に向けた研究開発が行われるようになります。アメリカ・イギリス・日本・西ドイツ・フランスなどで試作・実用化され、現在では自動車や航空機、産業機械を中心に用いられています。更に、異種材料の組み合わせや径・形状の自由度を高める研究が各国でなされています。
2. 摩擦圧接の原理
回転摩擦接合(RFW)は一般的には単に摩擦圧接と呼ばれており、大別するとブレーキ法とフライホイール法の二方式があります。
ブレーキ法は一方を固定、もう一方を回転させて推力によって加圧することで擦り合わせ、摩擦熱を発生させて接合する方式です。摩擦熱が十分となったとき、強制的に回転を止めるとともに推力を増加させ接合を完了します。摩擦時間又は寄り代(摩擦が生じる間に消耗する母材の長さ)を制御することで接合精度を高めることができます。フライホイール法は1964年のアメリカで開発され、一方を固定、もう一方に回転エネルギーを与え推力によって加圧するとともに摩擦仕事により回転が自然停止(慣性力)することで接合を完了します。フライホイール式はブレーキ式より操作が簡単で、圧接時間が短いことが特徴です。主にアメリカを中心に採用されています。
弊社では、ヨーロッパや日本で一般的に普及している接合精度の高いブレーキ法を採用しており、ここではブレーキ法の工程について解説します。
【ブレーキ法の工程】
A) 素材接触(接触位置測定⇒回転接触⇒加圧)
まずは、接合する材料の接触位置を測定するため、材料同士を突き合わせて接触位置を確認します。その後、一方を回転させ材料同士を突き合わせ加圧します。
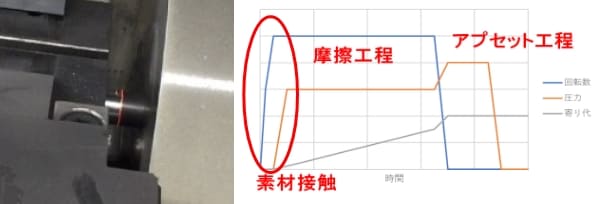
B)摩擦工程(回転・圧力を維持)
回転と加圧により摩擦熱が生じます。当工程で材料が軟化・変形し接触した表面がバリとして押し出されます。酸化被膜や汚れ等の接合を阻害するものが取り除かれ、接合が容易である新生面が作られます。
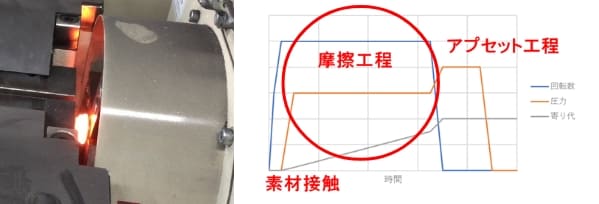
C)アプセット工程(回転停止⇒加圧⇒接合)
回転を停止し、摩擦工程での圧力よりも高い圧力(アプセット圧力)を加えることで接合が完了します。
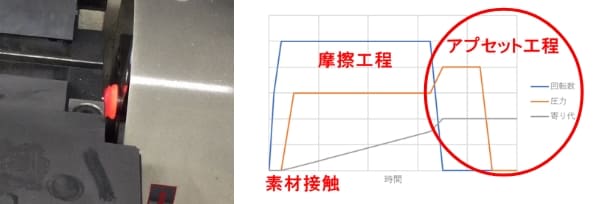
ブレーキ法による摩擦圧接では、摩擦工程時の回転数及び圧力と時間又は寄り代、アップセット工程時の圧力と時間を制御することで、圧接強度を最大限に高めます。
一例として、圧接機や材料の形状や大きさなどにより異なりますが、SUS304φ12丸棒同士の接合の場合、回転数:2500~3500 rpm、摩擦圧力:40~60 MPa、アプセット圧力:95~115 MPa、時間:2.5~4.5sで設定されます。
3. 摩擦圧接の強み
適材適所
低い接合温度によって金属間化合物が生じにくく,異種金属の接合が可能です。 異種金属や異形状で接合することで必要な箇所に必要な特性を持たせることができ、必要な部分に必要な材料を使用できます。例えば、丸棒と丸棒の間に軽量な材料や中空のパイプ材を挟めば軽量化するといったことが可能です。
形状は一方が円形(パイプ形状も含む)断面であり、回転トルクに耐えうるチャッキングが可能であれば治具次第で対応することができます。
高い強度を発揮
十分な摩擦圧力の下で圧接を実施すれば、摩擦面近傍で微細組織が得られ、面全体同士で接合します。普通溶接では円周部のみ接合されるため接合面に不溶着部が生じますが、接合面全体で接合する摩擦圧接ではこのような箇所は生じず、高い接手強度を得ることができます。材料や形状によっては母材と同等の接手強度となり、引張試験において母材側で破断することがあります。
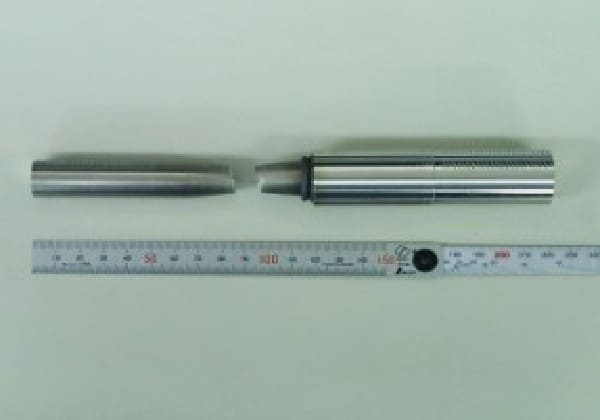
環境配慮型
摩擦熱以外の熱源が不要で熱損失が少ないためエネルギー効率が良く、スパッタ・ヒューム等の有害物質も発生しません。また、普通溶接に必要な溶接棒やフラックスなどの消耗品も不要です。
再現性
接合面以外の熱影響部が少ないため、熱による母材の変形が小さく、また接合条件を数値管理で制御できるため,作業は熟練を必要とせず再現性があります。
4. まとめ
【長所】
-
エネルギー効率が良い
接合に必要な温度が母材の融点以下であり、熱影響部が小さい。 -
不溶接部が生じない
接合面は常に閉ざされており、酸化・窒化の恐れはなく不溶着部も生じません。 -
変形が少なく、寸法精度が良い
接合面以外の熱影響部が少なく、溶接変形が小さい。 -
異種材質の接合が可能
種類の異なる材料の接合が可能です。 -
再現性があり安定度が高い
接合条件を数値管理できるため、熟練を必要とせず再現性があります。
【制約】
-
一方は円形で、回転に耐えることができること
-
母材に適した容量の圧接機が必要(大は小を兼ねません。)
-
細径、極太径、薄肉の接合は困難(圧接機の選定、試作での条件設定が必要です。)

環境にやさしい
省エネ:摩擦熱以外の熱源は不必要で、エネルギー効率が高い
省施工:溶接棒やフラックスなど接合に必要な消耗品が不要で工数を削減
無害:スパッタやヒューム、ガスなど有害物質が発生しない
コストダウンに適している
一体物からの削り出しと比較して材料費・加工費を削減
開先加工やインロー加工などの前工程を合理化し、加工工数を削減
必要な部分のみ高価な材料を使用するなど材料費を削減
素材重量を最小限に抑えることで歩留まり率を向上
異種金属結合の一般的な組合せ例
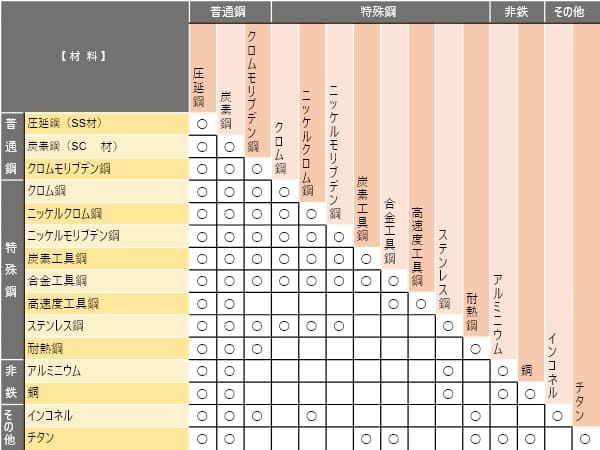